Pour fabriquer de l'acier, plusieurs éléments sont nécessaires, notamment du minerai de fer, du charbon ou du coke, ainsi que d'autres matériaux que l'on vous présente ici.
au sommaire
Le fer, la fonte et l'acier sont souvent confondus, il est donc important de d'abord les définir. Le fer est un élément chimique entrant dans la composition des deux autres. La fonte et l'acier sont fabriqués essentiellement à partir du mineraiminerai de fer mais contiennent également d'autres composants et sont différenciés par leur teneur en carbone : la fonte en contient de 2,1 à 6,6 7 % et l'acier de 0,03 % à 2 %.
Le principe de fabrication de l'acier
Pour fabriquer de l'acier, il faut du minerai de fer, du charboncharbon, de la chauxchaux et des ferro-alliagesalliages : aluminiumaluminium, chromechrome, manganèsemanganèse, siliciumsilicium, titanetitane, vanadiumvanadium... Ces derniers confèrent à l'acier des caractéristiques particulières adaptées à ses divers usages : architecture, ameublement, machines-outils, conditionnements alimentaires, etc. La fabrication nécessite aussi beaucoup d'eau pour le refroidissement des installations, la température de fusionfusion dépassant 1.500 °C.
L'acier peut être confectionné dans deux types d'usines : dans un haut fourneau, à partir du minerai de fer et de cokecoke (du carbone presque pur extrait du charbon), ou dans un four électrique, à partir d'acier de récupération (acier de recyclagerecyclage).
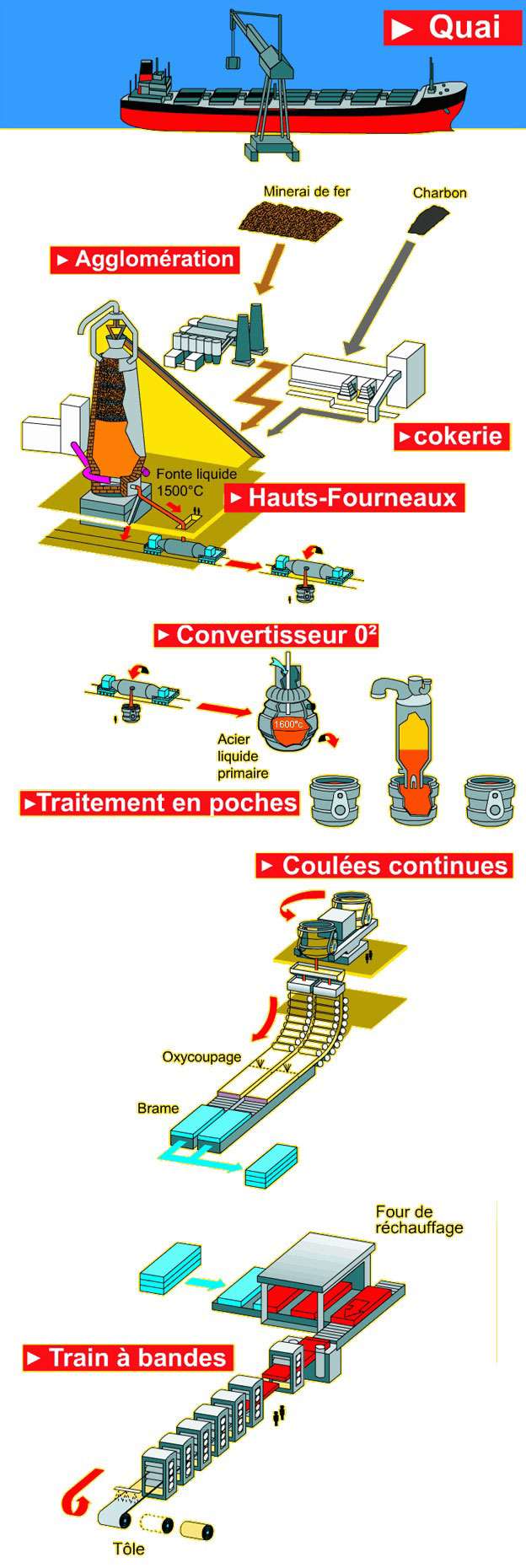
Le charbon fournit le coke servant de combustiblecombustible aux hauts-fourneaux où le minerai est fondu. Le métalmétal liquideliquide qui en sort est la fonte. Celle-ci est dirigée vers l'aciérie dans des wagons, appelés « poches-tonneaux », capables de maintenir sa température plus de 48 heures durant. Arrivée à destination, la fonte est mélangée à de la ferraille dans une grosse marmite, ou convertisseur. Le tout est oxygéné pendant 15 minutes, délai au bout duquel on obtient l'acier de base.
C'est à ce stade qu'est concoctée la préparation finale en dosant de façon précise les ferro-alliages. De nombreux prélèvements sont effectués et analysés tout au long du processus, jusqu'à l'obtention de l'acier désiré. On procède ensuite à la coulée continue (dans une lingotière) qui consiste à solidifier le métal sous la forme d'une longue bande.
Pour finir, la bande est découpée au chalumeau afin d'obtenir des brames : parallépipèdes épais de 20 centimètres, larges de 1,50 mètre et longs d'une dizaine de mètres. Pesant environ 25 tonnes, chaque brame sera laminée et formée en bobine. Bilan d'énergie griseénergie grise : 60.000 kWh/m3.
Les étapes de la fabrication de l'acier
- La formation de la fonte : le minerai de fer et le coke sont introduits dans le haut fourneau par le haut, la chaleurchaleur provoquant la combustioncombustion du coke et l'élimination des éléments chimiques contaminants. Le fer se charge ensuite de carbone au cours de sa descente et se transforme en fonte, qu'il faut alors séparer d'un mélange de déchetsdéchets appelé laitier.
- La conversion de la fonte en acier : la fonte en fusion est ensuite versée sur de la ferraille dans un convertisseur à oxygèneoxygène où de l'oxygène est insufflé pour éliminer le carbone sous forme de CO2.
- L'affinage : l'acier obtenu est affiné en ajoutant des éléments (nickelnickel, chrome...)) pour former différents alliages et modifier les propriétés mécaniques de l'acier en fonction des besoins.
- La coulée : l'acier est refroidi progressivement jusqu'à solidificationsolidification.
- Le laminagelaminage : l'acier est à nouveau monté à température pour le rendre malléable. Il est ensuite aplati dans des laminoirslaminoirs et la forme voulue lui est donnée.