au sommaire
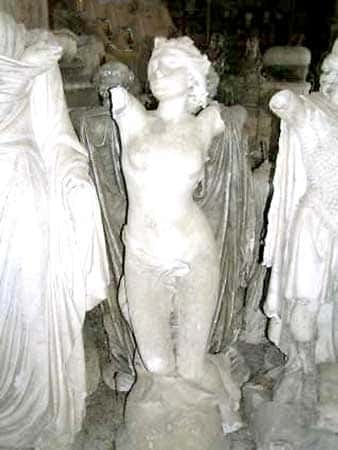
Sommevoire, Dommartin et la fonte
Le "Paradis" de Sommevoire rassemble une collection unique de modèles en plâtreplâtre issus de l'usine de fonte d'art de Sommevoire (aujourd'hui G.H.M.)). Le nom de "Paradis" était employé par les ouvriers au 19ème siècle en raison du grand nombre de statues de saints. Les modèles nous rappellent que partout dans le monde on trouve des statues, des fontaines, des bustes issues des fonderies d'art de Haute-Marne. L'ensemble de la collection était abandonné et promis à la destruction, mais en 1988 l'association des Compagnons de Saint Pierre et la municipalité de Sommevoire sauvent ce témoignage unique du patrimoine artistique haut-marnais. Le "musée" de Sommevoire présente plus de 600 modèles dans une ancienne grange, en attendant un espace consacré à la fonderie d'art de plus grande envergure.
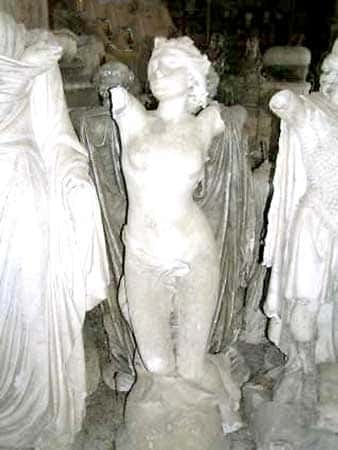
Moule de coulée de Sommevoire
A Dommartin-le-Franc la tradition métallurgique est très ancienne : un parchemin de 1264 concernant l'abbaye de Montier-en-Der fait mention d'une forge dans ce village. Un haut fourneau est attesté en 1773 ainsi qu'une affinerie, des lavoirs et des bocards. Le deuxième haut fourneau est construit en 1834 à l'emplacement de l'ancienne affinerie. Il y aura un troisième haut fourneau en 1837. Les hauts fourneaux sont éteints vers 1890 et l'entreprise se consacre au moulage de deuxième fusion comme "l'usine du bas" qui est l'autre entreprise métallurgique de Dommartin-le-Franc. Actuellement seule l'usine du bas conserve une activité, et un magasin de fontes d'art. L'usine du haut abrite un musée d'objet d'art en fonte et des expositions régulières autour d'un haut fourneau.
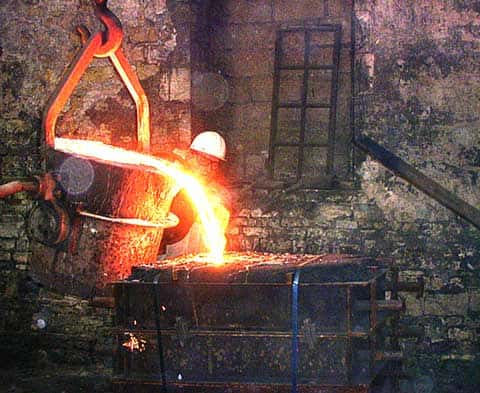
Coulée de fonte à Dommartin
Les fontes, histoire et technique.
Parmi les créations humaines, l'utilisation des métauxmétaux et la possibilité de les fondre, marque une étape décisive (âge du bronze 3000 ans avant Jésus-Christ) dans la maîtrise de la matière. Dès l'origine, la fabrication consiste à couler un métal ou un alliagealliage dans un moule, afin d'obtenir, après solidificationsolidification, une pièce dont les formes reproduisent celles du moule. Grâce à ce procédé, pourront être mis en forme des produits métalliques aussi divers que la fonte, l'acieracier, l'aluminiumaluminium, le cuivrecuivre, le zinczinc, le magnésiummagnésium, le plombplomb, le titanetitane, etc. Leur nombre ne cessera de s'accroître.
Dès l'apparition du travail du ferfer, les fondeurs firent preuve d'une maîtrise exceptionnelle de la technique de moulage comme le montre les roues de char coulées en bronze d'un seul jet ou les cloches transformées en véritables instruments harmoniques aux cours des X et XI siècles.
Jean-Baptiste GODIN dépose en 1840 son premier brevet protégeant les innovations de son poêle en fonte révolutionnaire de par sa robustesse, sa fiabilité, son élégance et son prix modeste. Un succès qui ne se démentira pas pour celui qui n'aura de cesse d'améliorer aussi les conditions de travail et de vie en construisant pour ses ouvriers le « Familistère de Guise » qui abritera jusqu'à 1 770 personnes.
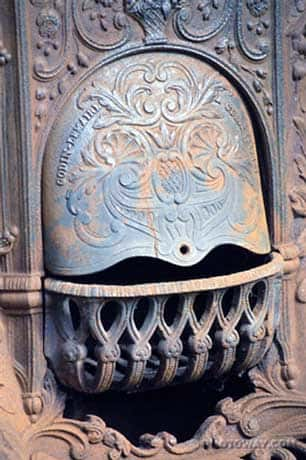
Godin en fonte
En 1899, Paris lance un concours d'architectesarchitectes pour la réalisation des entrées du métro dont la constructionconstruction va démarrer. Hector GUIMARD, dans la mouvance de l'Art Nouveau, fait preuve d'une inventivité exceptionnelle et propose une décoration réalisée en fonte.
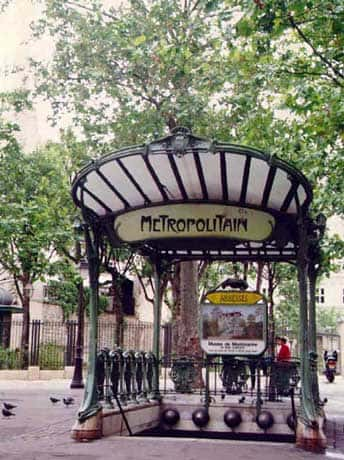
Métro de Paris, entrée à décor de fonte
L'industrie française de la fonderie se situe au 7ème rang des producteurs mondiaux derrière la Chine, les Etats-Unis, la Russie, le Japon, l'Allemagne et l'Inde. Avec 2,5 millions de tonnes produites, elle occupe le 2ème rang européen dont elle représente 19% de la production totale européenne.
La fonderie est un secteur assez fortement exportateur (en valeur : 31%, en volumevolume : 36%), principalement vers l'Union Européenne (69%), dégageant ainsi depuis de nombreuses années un excédent commercial. En 2004, il a atteint 0,45 milliard d'euros.
Production pièces moulées dans le monde en 2004 (en milliers de tonnes métriques)
- Fonte : 1 943 503
- Acier : 114 986
- Fonte d'alliages légers : 348953 parmi lesquelles les fontes d'aluminium
- Autres métaux non ferreux : 58217
- Total : 2 465 659 tonnes
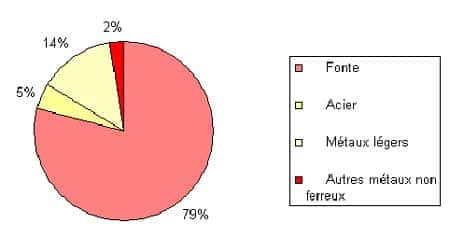
Chiffre d'affaire par alliages qui nous montre l'importance de la fonte
Quelques applications des fontes, les exemples sont innombrables nous n'en garderons que quelques-uns :
- marmites en fonte
- plaques de voirie, grilles,
- robinets en fonte ou en acier,
- cuves pour laiteries, brasseries, vinification, méthaniersméthaniers...
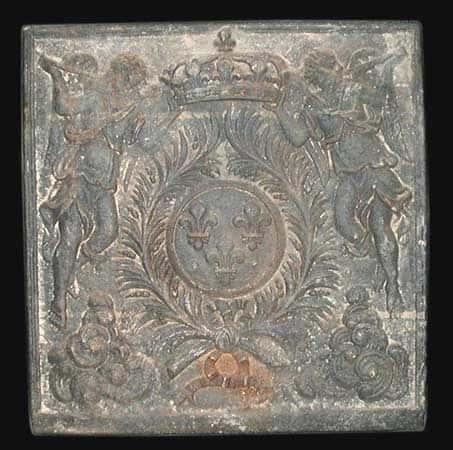
Plaque de cheminée en fonte
- les "trucks" de "skateboard",
- MotoMoto :
- Pas de voiture sans fonderie !
Les pièces moulées représentent 16 % du poids total d'un véhicule (dont 9% en fonte et 7 % en aluminium) ; autrement dit, l'automobileautomobile absorbe plus de 50 % des pièces produites par les entreprises de fonderie. La fonderie est largement présente dans les organes mécaniques, les châssis et les organes de liaison au sol. Ses caractéristiques sont requises dans nombres d'applicationsapplications : carters cylindres, pistons, vilebrequinsvilebrequins, culasse, volant, arbrearbre à camecame, culbuteurs, poussoirs de soupapes, turbocompresseurturbocompresseur, embrayages, boîtes de vitessevitesse, etc.
- Chemin de fer :
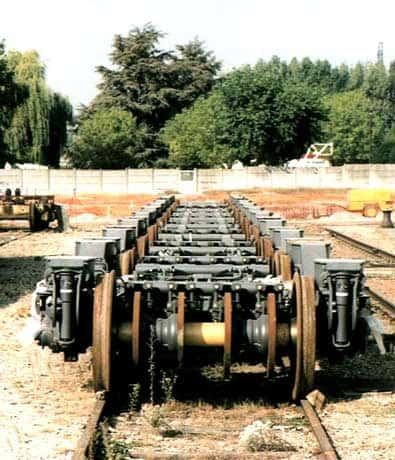
Bogie de TGV
- Tracteurs :
- Avions :
Les fontes moulées :
- les fontes phosphoreuses à graphite lamellaire
- Les fontes malléables avec un peu plus de carboneenviron 3%,
- Les fontes à graphite sphéroïdal avec plus de carbone -3,5 à 4%-
Les qualités de ces fontes les destinent à toutes sortes de pièces soumises à des efforts intenses et divers, des conditions mécaniques sévères....
Voir aussi à ce sujet le dossier sur : Le fer tombe le masque
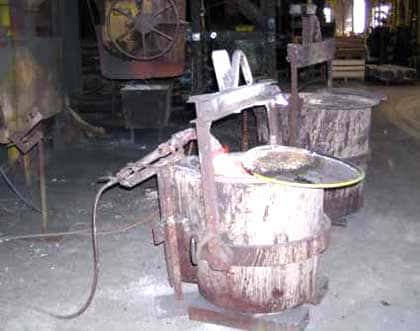
Godet de coulée
Deux procédés de moulage :
- Le moulage sablesable ou coquille :
- Le moulage sous pressionpression