au sommaire
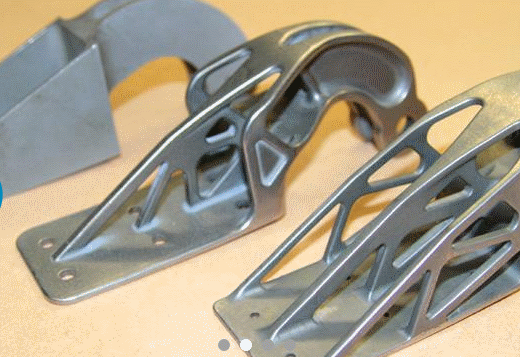
Ces charnières d'Airbus ont été imprimées en 3D. Le procédé permet d'alléger la pièce sans qu'elle perde en solidité. Imprimer de cette façon un satellite en une seule pièce, sans soudures ni boulons, est l'un des objectifs de l’Esa. Le gain financier serait énorme, et la structure plus robuste et plus légère. Il subsiste toutefois un obstacle : de petites bulles d’air viennent parfois s’immiscer lors de la fabrication. Un défaut que les 28 institutions et industriels participant au projet Amaze cherchent à réduire à néant. © EADS
Les imprimantes 3D sont, depuis quelques années, le ferfer de lance de l'universunivers de l'open hardware. Elles permettent de créer n'importe quelle pièce en plastiqueplastique par superposition de fines couches d'ABS. Futura-Sciences a d'ailleurs pu découvrir deux modèles pliables français, lors du Maker Faire européen qui se tenait à Rome, il y a une dizaine de jours. Actuellement, les industriels et de nombreux laboratoires d'institutions sont en train d'exploiter une variante de cette technique pour créer des pièces métalliques en 3D.
C'est le cas de l'Agence spatiale européenne (Esa) qui a réalisé une démonstration rapportée par la BBC, en marge d'une exposition sur l'impression en 3D au musée des Sciences de Londres. Ces imprimantes cumulent les avantages. Elles permettent de créer des pièces d'alliagesalliages métalliques de formes complexes qui ne pourraient pas être obtenues par les méthodes industrielles habituelles, comme l'usinage ou encore le moulage. De cette façon, nul besoin d'assembler deux éléments en les soudant ou en les boulonnant. La pièce est de facto plus légère et plus solidesolide. Il est également possible de créer des pièces capables de résister à des températures extrêmement élevées, comme les « divertors » en tungstènetungstène qui seront utilisés dans le futur Tokamak d’Iter à Cadarache. Ces éléments, capables de supporter des températures allant jusqu'à 1.000 °C, étaient d'ailleurs présentés par l'Esa à l'occasion de l'exposition du musée londonien.
Mais ce n'est pas tout, à l'avenir, lorsque certains défauts de jeunesse seront corrigés, cette technologie permettra d'obtenir une qualité de métalmétal inégalée. L'impression 3D métallique a un autre avantage de taille : elle permet de réduire à néant la perte de matériaux. Ainsi, alors qu'il faut consommer environ 20 kgkg d'acieracier pour créer une pièce pesant 1 kg, avec cette technique, seul l'équivalent du poids de la pièce est nécessaire.
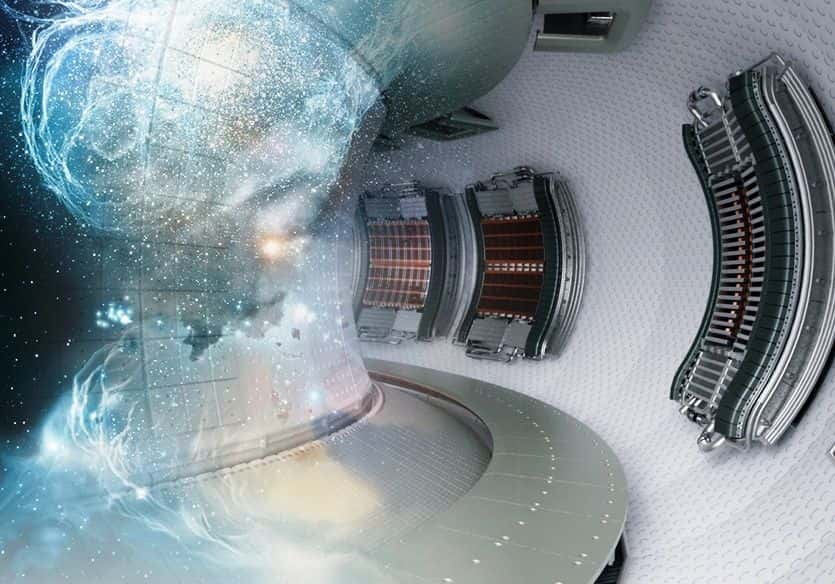
Le tokamak de l’Iter de Cadarache, sorte de boîte qui enferme l’équivalent d’un « mini soleil », nécessite des matériaux capables de résister à de hautes températures. Certains de ses éléments, tel le « divertor » conçu à partir de tungstène pour récupérer et recycler les déchets du plasma, peuvent être imprimés en 3D. © CEA
Impression 3D : objectif zéro déchet métallique
L'impression 3D emploie la technique de fabrication par couches additives, autrement appelée fabrication additive. Tout comme pour l'impression de pièces en plastique, de minuscules couches de métal sont superposées, afin de créer un objet par empilement. Pour cela, deux technologies sont employées. Un rayon laserlaser puissant permet de créer une forme en soudant une poudre métallique par fusionfusion. L'autre technique est la fabrication additive à technologie EBM (Electron Beam Melting)) : au lieu d'un laser, c'est un faisceau d'électronsélectrons qui va chauffer la poudre métallique de façon à ce qu'elle se solidifie pour réaliser les couches. Cette méthode est bien plus rapide, mais moins répandue.
La démonstration de l'Esa s'inscrivait dans le cadre d'un projet plus global baptisé Amaze (pour Additive Manufacturing Aiming Towards Zero Waste & Efficient Production of High-Tech Metal Products). Il s'agit d'utiliser les atouts des imprimantes 3D pour produire de façon efficace des pièces métalliques, avec le souci du « zéro déchetdéchet ». En tout, avec l'agence spatiale, ce sont 28 institutions et industriels (universités, Airbus, Astrium, EADSEADS, etc.) qui participent à ce projet. Des unités de production sont même en cours de déploiement dans différents pays du continent européen (Allemagne, France, Italie, Norvège, Royaume-Uni).
Et c'est du concret, puisque les premières pièces métalliques issues de ce projet ont déjà été produites, notamment des éléments de moteur, et même des sections d'ailes d'avion allant jusqu'à deux mètres de longueur. Mais il reste encore un cap à franchir pour que ces imprimantes 3D puissent fabriquer des pièces métalliques de qualité industrielle. En effet, les chercheurs butent toujours sur un phénomène qui rend parfois poreuses les pièces en raison de la présence de petites bulles d'airair. Un écueil que le projet Amaze vise à surmonter.