au sommaire
L'impression 3Dimpression 3D s'imposera sans doute progressivement sur des marchés de niches liés à la production de pièces uniques à forte valeur ajoutée, voire en très petites séries. Ce sur-mesure colle parfaitement aux besoins de l'industrie spatiale. Ainsi, Thales Alenia Space a récemment annoncé que les satellites de télécommunication Koreasat 5A et Koreasat 7, en cours de fabrication, embarqueront les plus grandes pièces pour le spatial jamais réalisées en Europe en fabrication additive à lit de poudre. « Il s'agit des supports d'antenne TM/TC en aluminium, pièces jumelles qui ont été fabriquées dans un même lot par la même machine », nous explique Florence Montredon, coordinatrice Développements en fabrication additive chez Thales Alenia Space (TAS).
Un support d'antenne de ce type est « d'ores et déjà en orbite depuis avril 2015 à bord du satellite de télécommunication TurkmenAlem », et le satellite Arabsat-6B, lancé depuis Kourou mardi 10 novembre 2015, « emportera également des tripodes issus de la technologie 3D ». D'autres pièces imprimées sont prévues, « en particulier sur chacun des satellites de télécommunications que nous avons actuellement en phase de design. Ce sont principalement des pièces d'interfaces, typiquement des supports d'antenne ou des ferrures de réflecteurs, en aluminium ou en titane ».
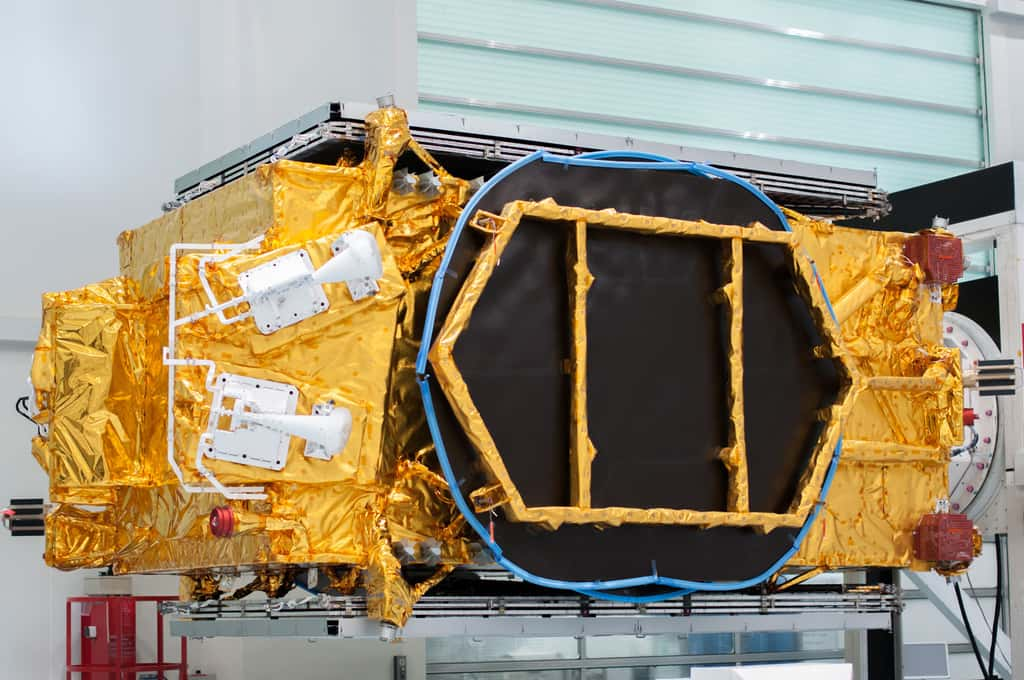
Le satellite TurkmenAlem utilise un support d'antenne imprimé en 3D. Il a été lancé en avril 2015 par un Falcon 9 de SpaceX. © Rémy Decourt
À l'avenir, TAS envisage d'utiliser de façon régulière cette technologie. D'ailleurs, les cas d'applications se multiplient et les « premières expériences pour le vol, réussies, permettent de généraliser cette technologie sur des pièces où elle réduit le coût, le délai et la masse ». La fabrication additive est « la technologie rêvée pour le secteur spatial car elle est faite pour la réalisation de pièces en petites séries, voire uniques ». La fabrication additive imprime tout aussi facilement « une pièce basique qu'une pièce avec des courbes, des alvéoles ou des cavités ». De plus, le résultat plus léger, alors que le secteur spatial est friand de réduction de poids car le kilogrammekilogramme coûte cher au lancement.
Bientôt un satellite en 3D ?
La prochaine étape pourrait être la constructionconstruction de pièces plus importantes, « intégrant plusieurs fonctions (mécanique, thermique, électronique, RF...)) », voire une structure entière de satellite. « Cependant, il faut encore mener des développements importants pour en arriver là mais la fabrication additive est une technologie qui progresse vite. Il faudra aussi certainement revoir la façon de penser et concevoir un satellite. Le challenge se situe tout autant dans le processus de conception que dans la technique de production elle-même. »
À plus court terme, TAS veut « entrer dans une phase d'industrialisation de l'usage de la technologie et d'en élargir le champ d'applications à de nouveaux produits ou sous-systèmes (nouvelles fonctions et pièces mécaniques plus chargées), les pièces de plus grandes dimensions (d'autres technologies additives que le lit de poudre émergentémergent également) et enfin les nouveaux matériaux ». La société a déjà commencé à introduire des polymèrespolymères mis en œuvre en fabrication additive et cherche maintenant à développer avec ses partenaires des matériaux répondant aux besoins spécifiques du spatial en matièrematière de stabilité, en particulier pour l'observation et la science.
À nouvelles technologies, nouvelles contraintes. L'impression de pièces en 3D n'échappe pas à cette règle. « Même si le secteur spatial a sur certains points moins de contraintes pour l'introduction de cette technologie que le secteur aéronautique par exemple, la maîtrise des risques est de mise ». La technologie ne permet de toute façon pas de tout faire aujourd'hui, en tout cas de manière rentable. « Les coûts de contrôle sont pour nous très élevés compte tenu du niveau requis pour la qualité des pièces ». Il y a des progrès à faire de ce côté-là. Des systèmes de contrôle in situ directement installés sur les machines arrivent maintenant sur le marché et « pourront sûrement augmenter la compétitivité de la technologie pour les secteurs exigeants comme le nôtre ». La taille réduite des machines à lit de poudre, « celles qui permettent d'atteindre les géométries les plus complexes, est également un frein identifié pour les applications ambitieuses ».