L’acier galvanisé est un matériau aux multiples applications disponible sous forme de barres, de profilés, de tubes, de tôles… d'objets manufacturés de toutes natures et dimensions. On le choisit pour sa capacité à résister aux effets néfastes de la corrosion.
au sommaire
L'acier se compose pour l'essentiel de fer et d'un pourcentage de carbone, qui augmente sa duretédureté et sa résistance mécanique. Mais, en l'état, l'alliage peut s'altérer plus ou moins rapidement selon le milieu. Au contact d'un airair humide, de l'eau ou de certains agents chimiques, il se met à rouiller. Du fait de la corrosioncorrosion, le métalmétal perd ses propriétés et se fragilise. Les industriels recourent à la galvanisationgalvanisation pour le protéger de la rouille.
La galvanisation, une préservation mate ou brillante
Découvert en 1836 par l'ingénieur français Stanislas Sorel, la galvanisation consiste à recouvrir l'acieracier d'une couche de zinc protectrice. Le traitement se déroule en plusieurs étapes, selon les prescriptions de la norme NF EN ISOISO 1461. Son nom est un hommage au médecin et anatomiste italien Luigi Galvani, à l'origine du « galvanisme ».
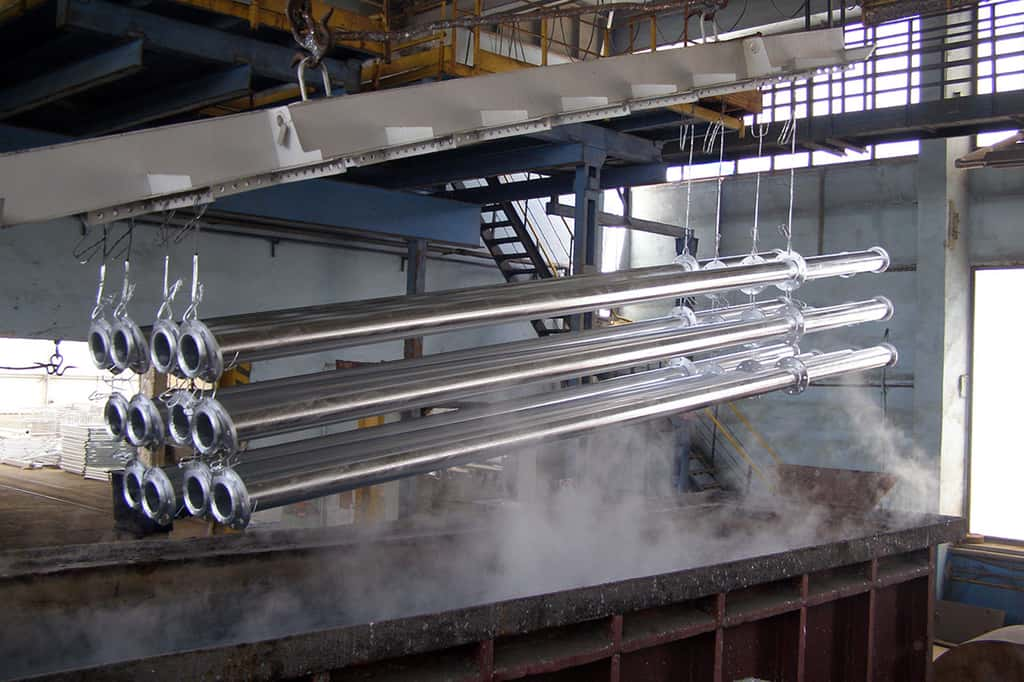
La galvanisation à chaud s’effectue par opérations de trempage successives. Plus la couche de zinc est épaisse, plus la protection est efficace et durable. © Weldon
Les pièces d'acier sont d'abord plongées 20 à 30 minutes dans un bain d'acide phosphorique, afin de les dégraisser. Elles sont ensuite décapées 2 à 4 heures durant dans des bains d'acide chlorhydriqueacide chlorhydrique. Cela permet d'éliminer les moindres traces d'oxydes et de calamines. Les pièces décapées sont rincées pour évacuer les produits chimiques des bains précédents. Puis on procède au fluxage. Il s'agit de déposer une première couche protectrice destinée à éviter une réoxydation de l'acier entre deux passages en cuve, tout en favorisant l'accrochage du zinczinc. Après séchage à 120 °C dans une étuveétuve, les pièces sont finalement galvanisées dans un bain de zinc en fusionfusion (450 °C). Elles sont mises à refroidir à l'air libre, avant d'être poncées pour enlever les aspérités. L'aspect final est mat ou brillant selon les usages prévus : constructionconstruction de maisons, industrie automobile, menuiserie métallique, fabrication d'appareils électroménagers, etc.